Concrete is the basic building material for modern high-rise buildings. It meets various architectural requirements by altering its properties with different additives. To ensure concrete quality, improve construction safety, and extend its lifespan, it is necessary to study the selection and addition methods of these additives for their reasonable use.
The construction industry considers concrete additives to be the fifth component of concrete. Using these additives can significantly improve concrete's density, strength, crack resistance, durability, and frost resistance. They also enhance concrete's workability, reduce curing time, lower labor intensity, and increase the mechanization of concrete construction. This results in higher construction efficiency, shorter project durations, and controlled construction costs. Additives effectively address concrete's inherent performance deficiencies, enabling the creation of high-strength, durable, and crack-resistant concrete, thus broadening its application scope.
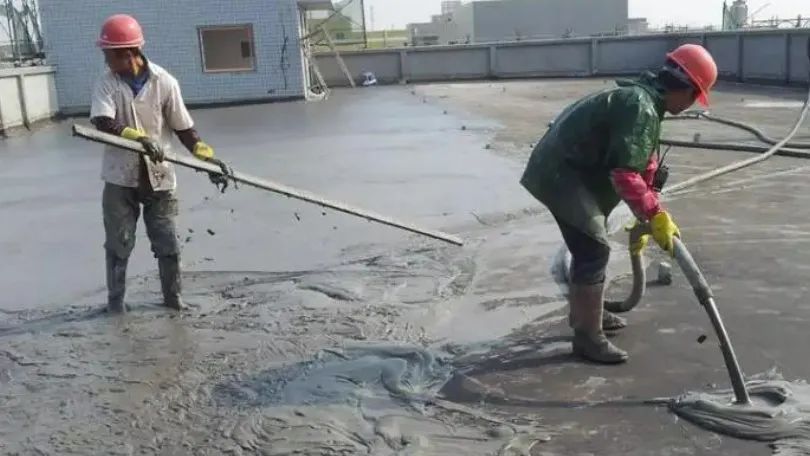
Application range of concrete admixtures
The application scope of concrete additives is extensive, as nearly all concrete projects utilize them to adjust concrete properties to meet construction requirements, enhance strength, or save cement usage.
During winter concrete construction, rapid temperature loss on the concrete surface may lead to temperature cracks. Early-strength agents or early-strength-type water reducers can accelerate concrete setting, reduce heat hydration, control internal and external temperature differentials, and mitigate concrete cracking tendencies.
In summer, for slipform concrete construction or large volume pours, retarders or retarder-type water reducers can delay internal heat hydration release, prolong concrete hydration reaction time, and prevent rapid temperature rises, effectively preventing cracking.
For shotcrete waterproofing and tunnel waterproof concrete construction, quick-setting agents expedite concrete congealing to enhance waterproofing capability. In densely reinforced large formwork prestressed concrete construction, efficient water reducers improve concrete workability, reduce water usage, and control heat hydration.
Underwater concrete construction benefits from air-entraining agents and water reducers for better workability and durability. High-grade and ultra-high-grade concrete require high-efficiency water reducers for formulation. Large-volume concrete utilizes expansive agents to counteract concrete shrinkage.
Prefabricated concrete components use additives to reduce preparation and curing time, accelerate production efficiency, optimize compaction processes, and improve component quality.
Misconceptions about the use of concrete additives include:
Purchasing low-cost additives:
Concrete mixing stations sometimes opt for cheaper additives to cut costs, compromising quality and performance standards, leading to inadequate performance of the additives.
Additive dosage control:
To manage expenses, some mixing stations impose strict limits on additive and cement usage, constraining concrete mix design and ultimately affecting concrete performance.
Inadequate additive quality management
Some mixing stations neglect proper quality management of additives. Casual procurement, inadequate material testing upon arrival, and improper storage lead to the use of substandard additives, resulting in inconsistent concrete performance and compatibility issues, posing quality risks.
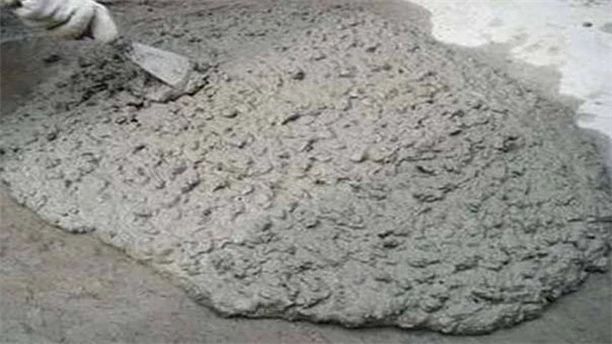
Correcting common misconceptions about the use of concrete additives:
Procurement Inspection:
Hire qualified and experienced procurement personnel to handle additive procurement.
Compare suppliers and prioritize reliability and reputation over low prices.
Establish long-term partnerships with reputable suppliers to ensure consistent quality.
Consider factors like production scale, transportation costs, technical expertise, and after-sales service when selecting suppliers.
Incoming Inspection:
Inspect additives upon arrival for quantity, specifications, and performance.
Verify factory technical documents and quality certificates.
Conduct on-site sampling and performance tests per national standards.
Reject additives that fail to meet quality requirements.
Routine Testing:
Conduct regular tests post-procurement to monitor consistency and performance.
Analyze any fluctuations in performance and compare with past results.
Report test results promptly to adjust mix designs based on material properties.
Validate mix designs regularly to ensure compatibility and performance.
Selection and Use:
Consider various factors such as cement type, aggregate properties, mix design, and environmental conditions when selecting additives.
Choose additives that significantly improve concrete performance without adverse effects.
Ensure stability, homogeneity, and non-corrosiveness towards embedded reinforcements.
Regularly validate mix designs to ensure effectiveness and performance.
Concrete additive quality inspectors must strictly adhere to established concrete mix designs and follow dosage requirements when adding additives. Prior to concrete construction each day, inspectors should sample and test the moisture content of sand, stone, and aggregates, adjusting water quantities accordingly based on material moisture content. They should also manage fluctuations in admixture and aggregate water reduction rates appropriately. If there are changes in material performance during concrete construction, such as increased aggregate demand or decreased admixture effectiveness, adjustments to the mix design must be made promptly. Increasing aggregate demand or decreasing admixture water reduction rates may necessitate an appropriate increase in admixture dosage to maintain the water-cement ratio and ensure concrete strength meets performance requirements.
While additives can significantly improve concrete properties and enhance economic benefits and technical performance, improper use can adversely affect concrete quality. Therefore, strict adherence to relevant standards, diligent routine testing of concrete additives, and timely adjustment of concrete mix designs based on test results are essential to ensure concrete quality.