The concrete industry is booming, and many are joining the family. Ready-mix concrete producers often face various challenges in their daily work. Today, I’ve gathered five common technical questions and solutions to share with everyone.
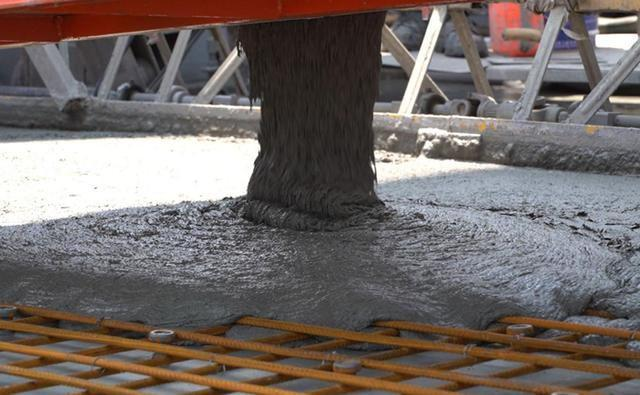
Question: How do you test the air content of water reducers?
Answer: Besides using an air content meter to measure the concrete's air content and infer the air-entraining capacity of additives, you can also use the following method: Take a 100 ml graduated colorimeter tube and add 4 grams of the powdered sample. Then, add water until the volume reaches 40 ml. Use a steel ruler to measure the vertical height of the solution (h0). Hold the stopper of the colorimeter tube tightly and shake it vigorously 20 times. Immediately start a stopwatch while measuring the height of the foam at the top (h1). Record the time (s) when the foam disappears, revealing the liquid surface. Control indicators: foam height < 45 mm, foam dissipation time < 50 s.
Question: What should you pay attention to when using air-entraining agents?
Answer: First, control the air content, which is usually between 2% and 4% (by volume). Otherwise, concrete strength will decrease. Also, avoid poor-quality air-entraining agents with large bubble diameters and spacing, such as sodium dodecyl sulfate or wood calcium. A slightly higher dosage can cause a significant drop in concrete strength. Conduct trials to determine the type and dosage before use.
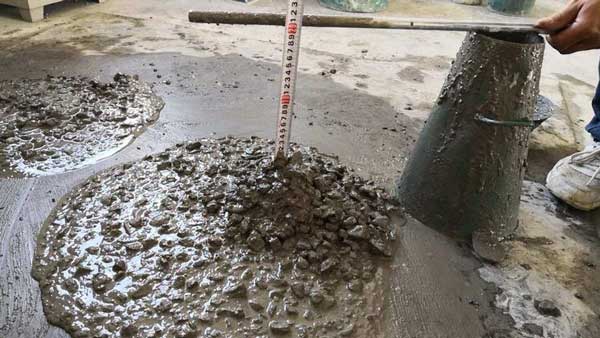
Question: If the mix is stable at the plant but segregates at the construction site, is it due to the aggregates or the additives?
Answer: The concrete mix design ensures that all indicators meet pre-design requirements and maintain a safety factor under experimental conditions. If segregation occurs during production, the materials’ properties or parameters may have changed. According to production quality management standards, retesting of key parameters for all raw materials is necessary before use, and adjustments to the mix design must be made based on the results. Generally, segregation of the mix is more related to water and additives. The segregation due to excess water appears as a diluted mix, while the primary function of additives is to separate the cement hydration flocs, resulting in the separation of the cement paste. Segregation due to improper aggregate grading is harder to identify in a flowing mix but becomes evident once the mix is stationary.
Question: Why does high-strength concrete sometimes stop gaining strength over time, even though the mix design and materials haven’t changed?
Answer: The properties and parameter indicators of the materials used in concrete are relative and may not be entirely consistent. If retesting the incoming materials shows no significant deviation from the standard, other factors should be considered. Besides the basic parameters of the materials, the strength of the concrete also depends on the compaction during forming and the curing conditions, such as temperature and humidity. If all the factors are within controlled limits, strength development will occur, but the rate of development may vary. The testing process can also affect the results. The condition of the test sample after failure and whether it meets regulatory standards is crucial, especially for high-strength concrete, which requires stricter testing protocols due to increased brittleness. In one case, confusion caused by removing the mold before labeling the samples led to inconsistent strength results.
Question: What are the main factors affecting concrete strength, and how do they impact it?
Answer: The main factors affecting concrete compressive strength are cement grade and water-cement ratio. Higher cement grades result in higher concrete strength. A lower water-cement ratio also leads to higher strength, provided the mix is well-compacted. The type, particle size, grading, and cleanliness of the aggregates also matter. Using larger, well-graded, and clean aggregates reduces the water-cement ratio and increases the interfacial bond strength, resulting in higher concrete strength. Curing temperature and humidity also play a role by affecting the cement’s hydration and hardening. Ideal temperature and humidity accelerate strength development, while adverse conditions hinder it. The age of the concrete is another factor; longer curing times allow more complete hydration, reducing porosity and increasing strength. Lastly, construction methods, particularly mixing and compaction, significantly influence concrete strength. Strong mechanical mixing and compaction result in higher strength.