In this article, we will briefly explore concrete slump and methods to test concrete slump. This will help us use concrete admixtures and improve our work in the future.
Definition of Concrete Slump
Concrete slump refers to the plasticity and pumpability of concrete. Factors affecting slump include changes in gradation, water content, weighing deviations of scales, admixture dosage, and often overlooked factors like cement temperature. Slump measures the workability of concrete, ensuring smooth construction. It reflects properties like water retention, flowability, and cohesion. Slump is quantified to assess whether construction can proceed normally.
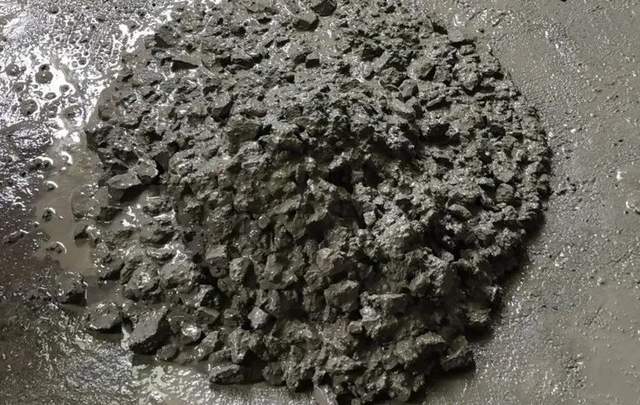
Workability refers to how easy it is to work with and compact the concrete evenly. It is a combined performance index that includes flowability, cohesion, and water retention. Factors affecting workability include the amount of water per unit volume, water-cement ratio, sand ratio, cement type, aggregate conditions, admixtures, time, and cement temperature.
Importance of Concrete Slump
Slump is a critical indicator of concrete performance. It is one of the key parameters that reflect the flow characteristics of concrete. A higher slump indicates better flowability, making the concrete easier to place and fill into molds. Conversely, a lower slump suggests reduced flowability, making construction more difficult.
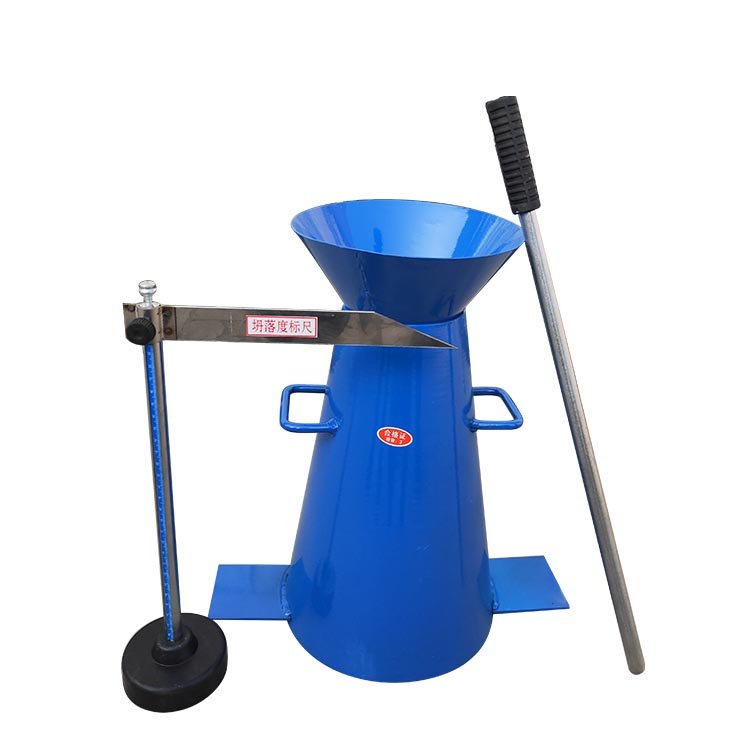
Slump values relate to the strength and durability of concrete. Excessive slump can reduce both strength and durability and may cause shrinkage and cracking, leading to quality issues. Large construction projects often require slump to be controlled within specific ranges to ensure concrete quality and performance.
Simply put, slump indicates whether freshly mixed concrete is easy to work with. Why control slump during construction?
- Convenience: It is simple to use and easy to promote in construction. No other test method is as straightforward as the slump test for assessing concrete workability.
- Quality Control: Slump is also a way to control concrete quality. Every mix design has a target slump value. During construction, you need to control the slump according to this value to ensure consistency.
Concrete Slump Testing Method
- Test Tools: Standard metal slump cone, bullet-shaped tamper rod, shovel, ruler, trowel, scale, etc.
- Test Steps:
- Wet the slump cone and other tools. Place the cone on a non-absorbent, rigid horizontal surface. Step on the footrests to hold the cone in place.
- Fill the cone with concrete in three layers, each layer compacted to one-third of the cone’s height. Use the tamper rod to compact each layer 25 times, spiraling from the outside toward the center. Ensure the rod reaches the bottom in the first layer and penetrates the previous layer in the others. After compacting the top layer, level it off with a trowel.
- After cleaning any concrete from the edges, lift the cone vertically and steadily in 5–10 seconds. The entire process, from filling to lifting, should be completed within 150 seconds.
- Measure the height difference between the cone and the highest point of the slumped concrete. This difference is the slump value. If the concrete shears or collapses, take a new sample and retest. If this occurs twice, the concrete has poor workability and should be noted.
- Observe Cohesion and Water Retention:
- Cohesion: Lightly tap the sides of the slumped concrete with the tamper rod. If the cone gradually sinks, cohesion is good. If the slumped portion cracks or segregates, cohesion is poor.
- Water Retention: Evaluate based on the amount of thin slurry that seeps out. If a lot of slurry leaks from the bottom, exposing the aggregate, water retention is poor. If little or no slurry seeps out, water retention is good.
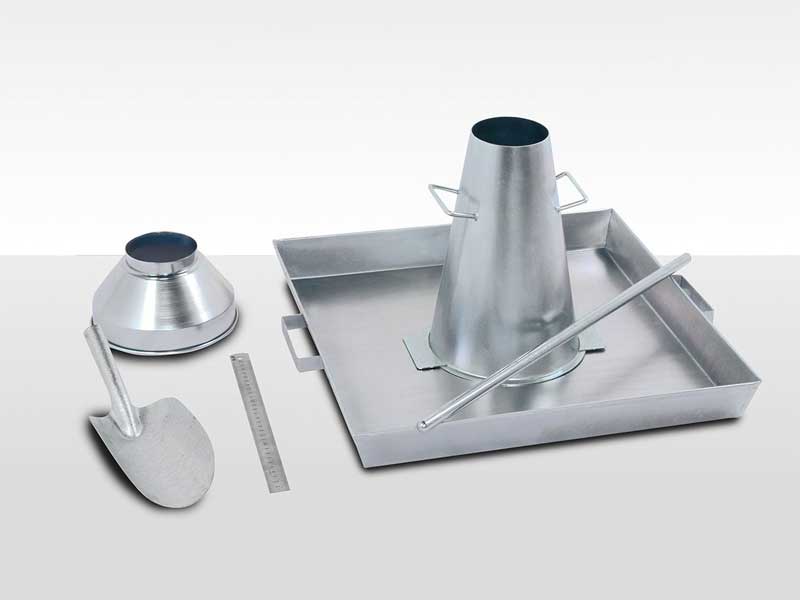
Standards for Concrete Slump
- For concrete with a strength grade lower than C50, slump should be less than 180 mm. For grades above C50, slump should exceed 180 mm.
- For specified slump values below 40 mm, the tolerance is ±10 mm; for slump between 50–90 mm, the tolerance is ±20 mm; and for slump greater than 100 mm, the tolerance is ±30 mm.
- The sampling frequency for slump tests should match the frequency of strength tests.
- Slump requirements should follow the construction contract.
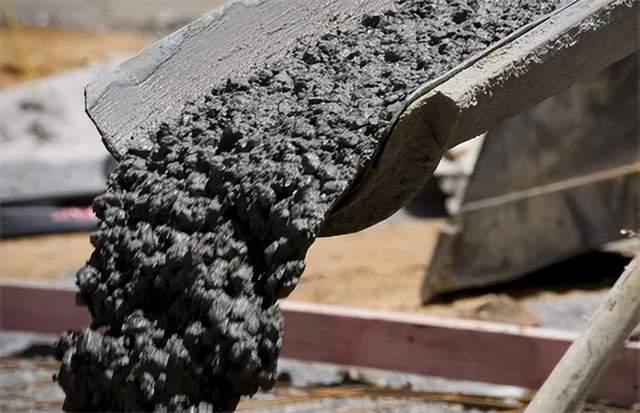