Concrete consists of cement, coarse and fine aggregates, water, additives, and mineral admixtures.Due to differences in the density and particle sizes of each component, as well as variations in the mix proportions, the materials may separate from each other under the influence of gravity and external forces. This phenomenon is known as concrete segregation.
In the mixture, larger and heavier coarse aggregate particles tend to sink quickly, settling at the bottom. On the other hand, water in the mixture, being lighter, rises and separates from the mixture, leading to the phenomenon of water bleeding on the surface of the concrete. Water bleeding is a manifestation of poor cohesion in concrete.
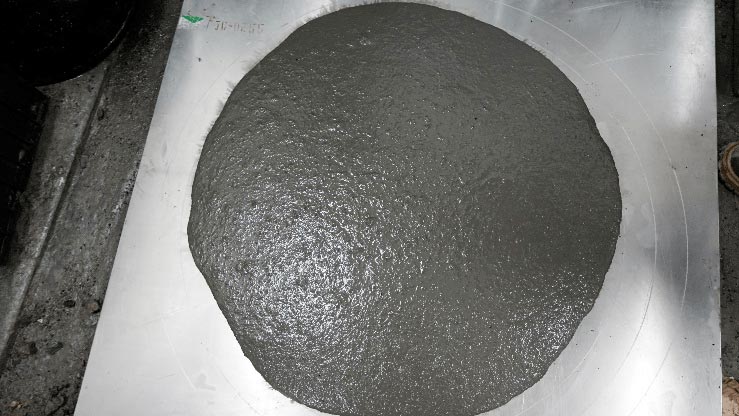
Concrete segregation generally manifests in two ways. One is when coarse aggregates in the mixture separate easily, indicating poor envelopment of the aggregates by the mixture. The other is when the mortar in the mixture separates easily.
We measure concrete's water-retaining capability by observing the extent of excess water or bleed water separation from the mix. When the slump increases, and excess water or thin mortar segregates at the bottom with aggregates exposed due to mortar flow, it indicates insufficient water retention in the mixture.
What are the causes of secretion
(1)A low content of C3A (tricalcium aluminate) in cement results in a longer setting time. Similarly, if the cement has a smaller specific surface area, it can also lead to prolonged setting time.
(2)Poor-quality fly ash, with high carbon content where carbon exists in a sponge-like form, can absorb water and additives. This leads to an increase in the amount of water required and, after vibration, some of this absorbed water is released, causing bleeding. Additionally, excessive use of mineral admixtures can also contribute to water bleeding.
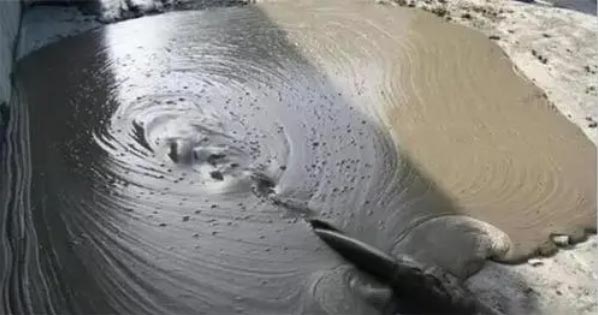
(3)The use of retardants like phosphates, citric acid, sugars, and glucose in pumping admixtures can easily lead to water bleeding. Additionally, using fatty acid-based high-range water reducers and amino sulfonate-based high-range water reducers can also intensify the occurrence of water bleeding.
(4)When the fineness modulus of sand is excessively high and the content of particles with a diameter of 0.315mm is less than 15%, the water retention of concrete decreases, leading to water bleeding. Additionally, if the apparent density of the coarse and fine aggregates is too high, it can also cause water bleeding to occur.
(5)Concrete with a low sand-cement ratio or insufficient cementitious material content (less than 300kg/m3) in high-slump concrete can result in water bleeding.
What causes concrete segregation
Water seepage is the prerequisite for concrete segregation. First, water seeps, followed by the separation of various components, leading to segregation. Severe segregation can block pumps during construction and impact the progress. Segregated concrete poured onto vertical structures like walls and columns can lead to structural delamination. In serious cases, a thick mortar layer devoid of coarse aggregates forms on the upper part of columns or walls. Pouring separated concrete onto slab structures can lead to settling and, consequently, the formation of hairline cracks.Concrete that exhibits water seepage, when poured onto vertical structures like columns or bridge piers, can lead to the phenomenon known as "sand streaks" upon formwork removal. Sand streaks occur due to the process of water seepage carrying away cement and other binding materials, leaving sand exposed.
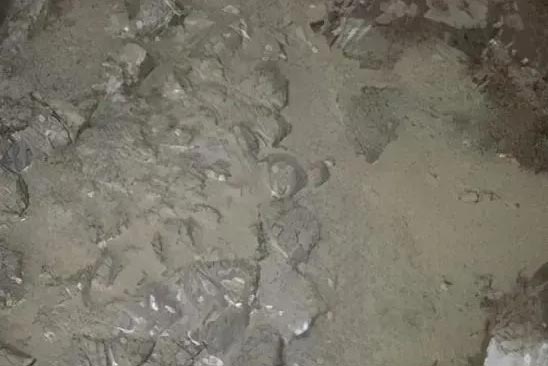
Segregation is caused by several factors:
(1) Coarse aggregate with excessively large particle size and discontinuous gradation, leading to settlement and segregation when the mixture is relatively still.
(2) Low sand-cement ratio in the concrete, resulting in poor cohesion.
(3) Excessive use of admixtures.
(4) Improper control of sand moisture content or water accumulation in the truck, leading to excessive water usage.
(5) Malfunctioning or improperly closed admixture valves, causing excessive admixture content and leading to segregation.

Severe separation happens when water is drained from the transport vehicle or if admixture valves malfunction or close inadequately. In such cases, discard the material. If segregation is moderate, pour off surplus mortar, then add thicker mortar with a strength grade at least two levels higher. Ensure thorough mixing, pass inspection before plant exit.
If unsuitable aggregates, oversized particles, or poor gradation lead to separation, consider adding fine aggregates during production, adapting to the specific situation.
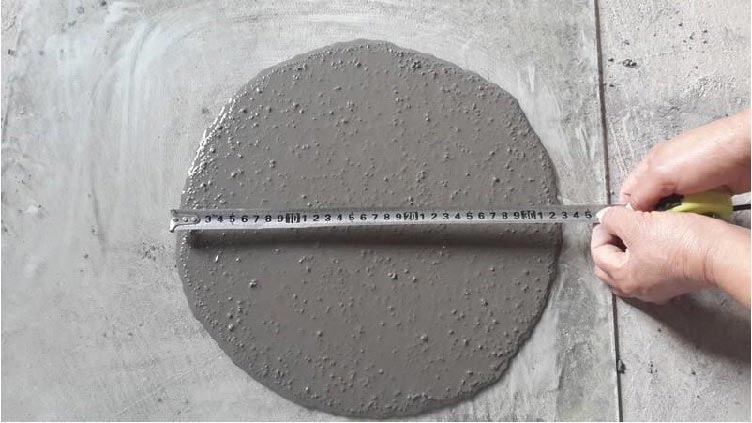
When segregated concrete is poured at construction sites, timely action should be taken based on the specific situation. In severe cases, prompt removal and re-pouring might be necessary. For slight segregation on slab structures, characterized by an excess of surface mortar, spreading fine aggregates and compacting them before the concrete sets can help alleviate the issue.