Polypropylene crack-resistant fiber is a reinforcement material for concrete. It is produced through a special process, giving it strong resistance to acids, alkalis, and low thermal conductivity. It has extremely stable chemical properties. Adding it to concrete significantly improves its crack resistance, impermeability, impact resistance, earthquake resistance, frost resistance, abrasion resistance, burst resistance, aging resistance, workability, pumpability, and water retention. This article explores the main characteristics and uses of polypropylene fiber. Using polypropylene fiber to its full potential ensures the successful completion of projects, benefiting humanity.
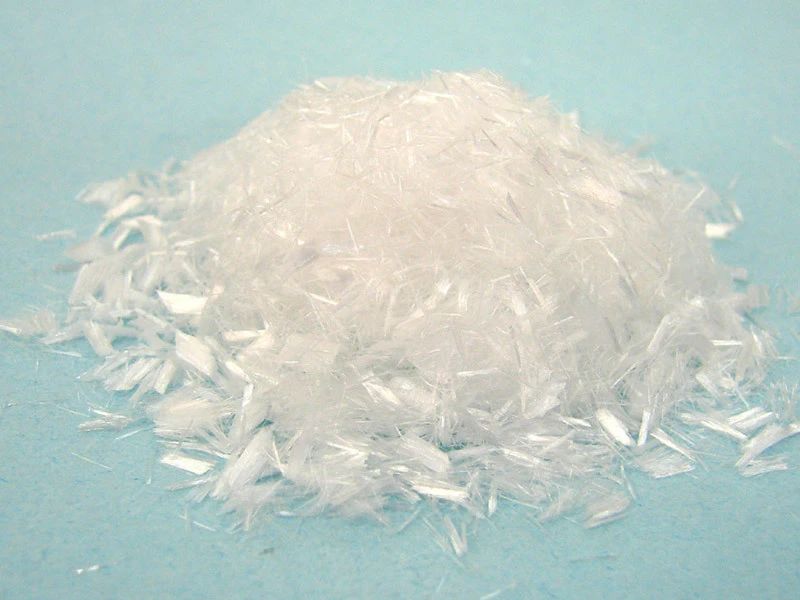
What is Polypropylene Fiber?
Polypropylene fiber is a synthetic fiber made from polypropylene, abbreviated as PP fiber. It has chemical resistance, heat resistance, electrical insulation, high mechanical strength, and excellent wear resistance. When added to mortar or concrete, it effectively controls micro-cracks caused by temperature changes during the early plastic shrinkage phase, preventing and inhibiting crack formation and development. This greatly improves the crack resistance, impermeability, impact resistance, and earthquake resistance of concrete.
It is widely used in waterproofing underground projects, industrial and civil construction projects such as roofs, walls, floors, pools, basements, as well as roads and bridges. It is an ideal new material for crack resistance, impermeability, and abrasion resistance in mortar and concrete projects.
Uses of Polypropylene Fiber
Polypropylene fiber is lightweight and corrosion-resistant, widely used in textiles, building materials, and insulation materials.
In construction materials, adding polypropylene fiber to concrete enhances its fracture strength and impact resistance, extending its service life.
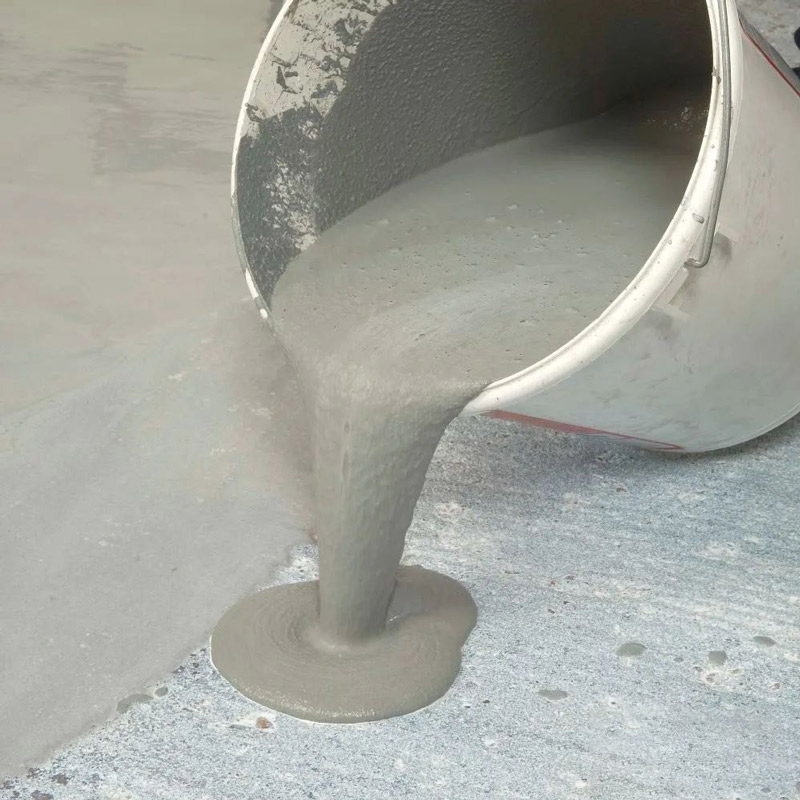
Polypropylene fiber can also be added to gypsum, enhancing its wear resistance and breathability.
In batteries, polypropylene fiber is often used as a separator.
Main Characteristics of Polypropylene Crack-Resistant Fiber
- Prevents cracks in concrete
- Improves impermeability of concrete
- Enhances freeze-thaw resistance of concrete
- Boosts impact, bending, fatigue, and earthquake resistance of concrete
- Improves durability and aging resistance of concrete
- Increases fire resistance of concrete
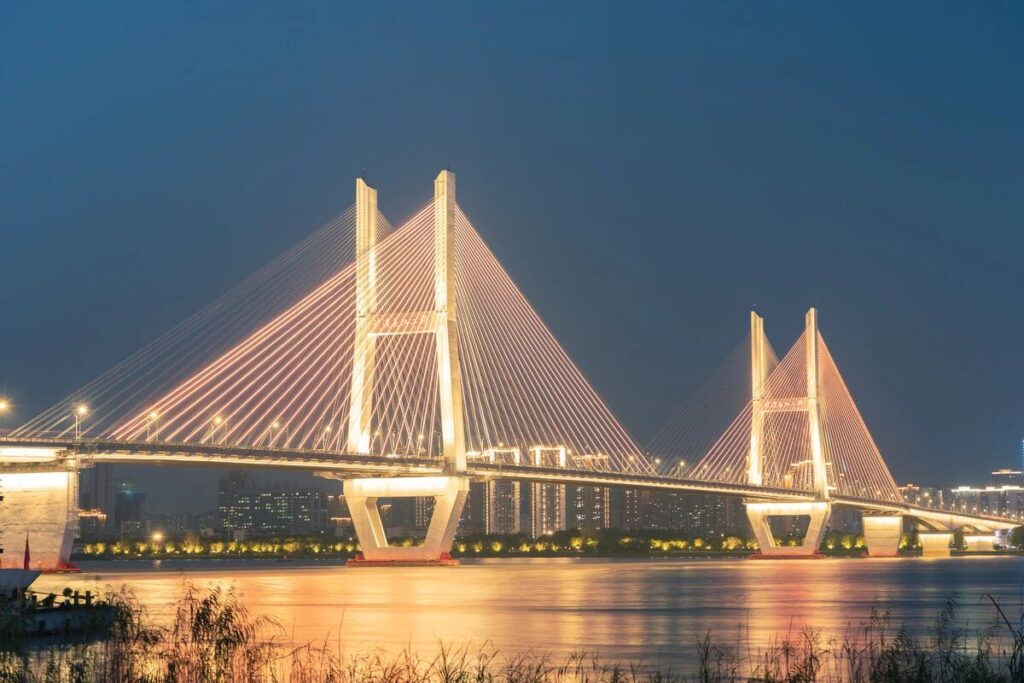
Applications of Polypropylene Crack-Resistant Fiber
- Rigid self-waterproof concrete structures: basement floors, walls, roofs, water tanks, etc.
- Projects with high crack resistance, impact resistance, and abrasion resistance requirements: hydraulic projects, subways, airport runways, ports, overpasses, bridge decks, piers, and long-span structures.
- Cement mortar: interior/exterior wall plastering, aerated concrete plastering, interior decoration putty, and insulation mortar.
- Explosion-proof and fire-resistant projects: civil defense military projects, oil platforms, chimneys, refractory materials, etc.
- Shotcrete: tunnel linings, culverts, thin-walled structures, slope reinforcement, etc.
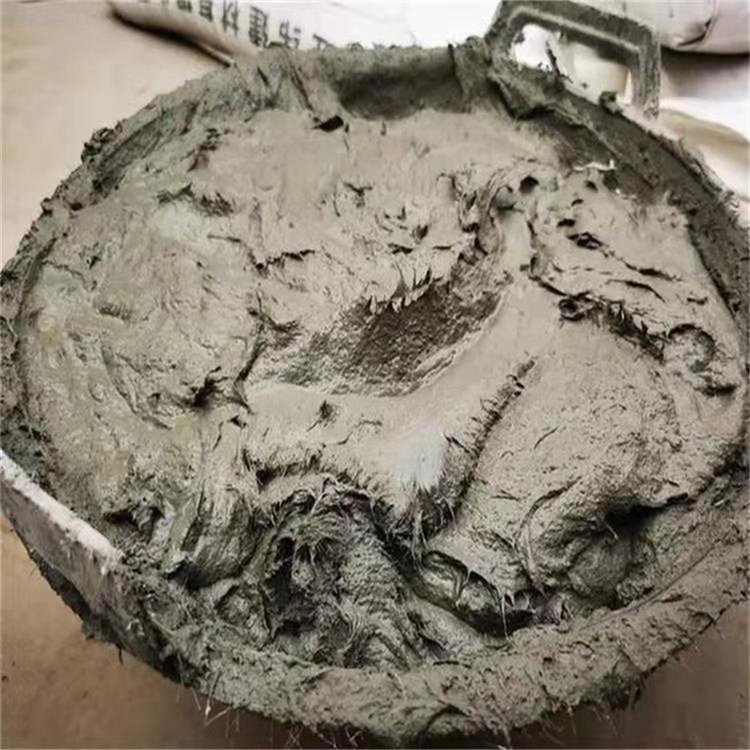
The application of polypropylene fiber in concrete is already widespread. Studies cover basic mechanical properties (compressive strength, tensile strength, flexural strength), workability, durability, and component beams and columns. The addition of fiber primarily enhances the toughness of concrete.
In conclusion, polypropylene fiber concrete has a promising application prospect.