In summer, the high temperature makes concrete construction relatively difficult. Today, let's learn about the common issues in concrete construction during summer!
Key points for quality control in summer concrete construction
- Strictly control the pouring temperature, ensuring it complies with the design specifications.
- The segmenting, jointing, block height, and interval time of concrete pouring should all meet the design and code requirements.
- To prevent cracks, comprehensive measures must be taken from structural design, temperature control, material selection, mix optimization, construction arrangement, construction quality, surface protection, and curing of concrete.
- To improve the concrete's crack resistance, it's necessary to improve the construction process. The quality of concrete should not only meet the strength assurance requirements but also meet good standards for uniformity as per relevant codes.
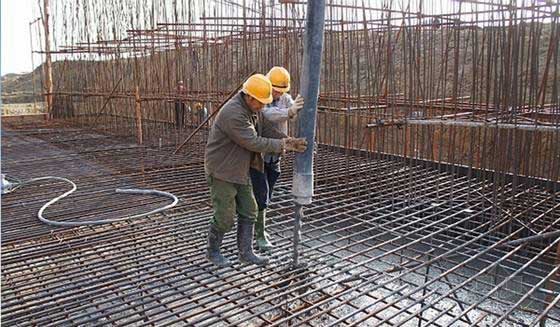
Measures during concrete mixing, transportation, and unloading
When mixing concrete, control the temperature to regulate the water content, reduce slump loss rate, and minimize plastic shrinkage cracking.
- During summer construction, keep the sand and aggregate temperatures below 25°C in the batching plant. Use cooling devices for mixing water, shade and insulate water pipes and tanks. Adding crushed ice to part of the mixing water helps control the temperature.
- Use water reducers to reduce cement content and increase aggregate size where pouring conditions allow.
- For long-distance transport of concrete mixtures, use retarders to control setting time. Ensure correct dosages, especially for large concrete areas to prevent surface hardening. Excessive retarders can cause surface hardening and rippling if finished too early.
- Use high-range water reducers for higher slumps. Some can maintain slumps for 2 hours, reduce friction between aggregate particles, and slow heat accumulation in the mixing drum.
- Consider using slag cement to replace ordinary Portland cement to reduce cracking in large concrete pours.
- Sprinkle water on aggregates to lower concrete temperature through evaporation, using cool water for better cooling effects, especially in high humidity.
- For long-distance transport in hot, humid weather, delay mixing in transit trucks to maintain mixing status on arrival.
- Plan pours to avoid high daily temperatures, preferring evening pours to reduce wind and temperature impacts. Concrete setting near sunrise when humidity is highest reduces early drying and cracking.
- Only adjust slump with design-specified water; avoid additional water on-site.
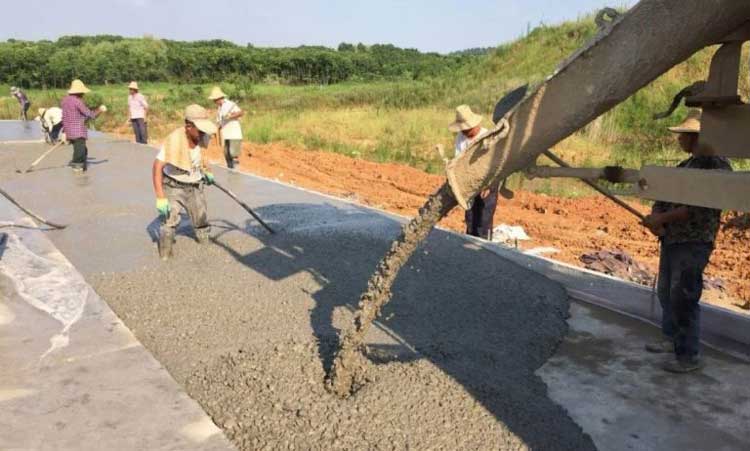
Measures for concrete pouring and finishing
- Prepare construction forms, equipment, and organize workers, paying special attention at the start of pouring.
- Use a thermometer to monitor concrete temperature on-site and request adjustments from the supplier if necessary.
- Protect tools, machinery, and materials in contact with concrete from direct sunlight, dampening and covering them before use if needed, and sprinkling for cooling.
- Dampen the base before pouring concrete on the ground.
- Dampen the edges of the formwork with cold water before pouring concrete.
- Plan summer concrete pours carefully, pouring continuously and rapidly, avoiding finishing while water is still present on the surface.
- If plastic shrinkage cracking is possible, control surface moisture evaporation, and promptly cover poured and finished concrete under dry conditions.
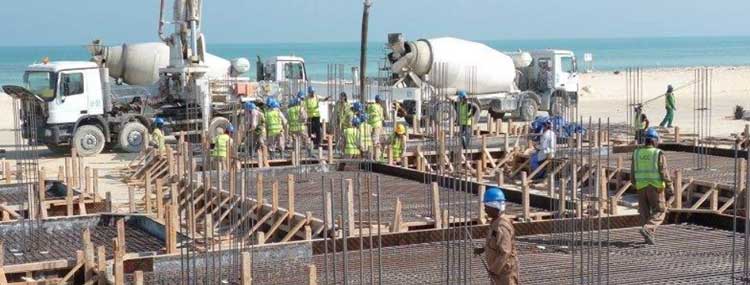
Maintenance of concrete poured in summer
Curing of concrete in summer is crucial to avoid strength reduction and surface issues like plastic shrinkage cracks. In hot, dry weather, inadequate curing can lead to rapid moisture evaporation, preventing proper hydration of cement particles, reducing bond strength, and causing surface flaking. Insufficient curing can also result in early shrinkage deformation, leading to cracking and compromising concrete durability and integrity. Immediate and continuous curing is essential post-concrete placement to prevent these issues.
- Start curing immediately after finishing or initial setting of concrete.
- Prioritize continuous water curing method for 1-2 days after pouring to ensure concrete remains adequately moist, adhering to national standards for curing duration.
- For large projects, curing compounds are practical and efficient. White curing compounds form a reflective film that reduces heat absorption, limiting temperature rise in concrete.
Summer Concrete Pouring Treatment Measures
- Pouring concrete in hot weather lowers final strength but accelerates setting and early strength gain. Increase water amount for the same slump requirement. Take actions like sprinkling water on aggregates to cool them, adding retarding agents to concrete, using ice instead of some mixing water, and adjusting cement content per cubic meter.
- Hot weather reduces concrete air content, affecting durability, workability, and mix volume. Regularly check air content and increase air-entraining admixture dosage.
- Hot weather drying of freshly poured concrete surface leads to insufficient finishing time, reduced surface weather resistance, and cracking. Adjust sand content, spray water using a mist sprayer if needed for finishing, promptly cure after finishing, use curing compounds early, maintain even slump within specified limits.
- Uneven drying and curing in the vertical direction cause rippled surface in concrete slabs. Use low-slump mixes and mist water lightly with a sprayer if rippling occurs.
- Uneven drying vertically during early curing results in slab warping. Use low-slump concrete mix, cure immediately after finishing with curing compounds that reflect sunlight, reduce surface temperature, prevent cracking due to temperature differentials, and cover with plastic film after concrete hardens.